Can Philippine manufacturing ever recover? The transition from Industry 1.0 to Industry 4.0
As we can read in the blog of Eric Howard entitled “The Evolution of the Industrial Ages: Industry 1.0 to 4.0,” modern industry has undergone great advances since its earliest iteration at the beginning of the industrial revolution in the 18th century (1770 to 1840).
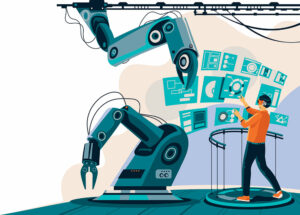
(Part 2)
As we can read in the blog of Eric Howard entitled “The Evolution of the Industrial Ages: Industry 1.0 to 4.0,” modern industry has undergone great advances since its earliest iteration at the beginning of the industrial revolution in the 18th century (1770 to 1840).
Previous to that game-changing economic event — literally for millennia — most of the goods consumed by human beings all over the world, which included weapons, tools, food, clothing and housing, were fabricated by hand or by using animals. These ancient practices changed at the end of the 18th century with the introduction of manufacturing processes. The progress from Industry 1.0 was then a rapid uphill climb that led to what is now called Industry 4.0 characterized by the digital age to which we belong. We will now briefly recount the transition from Industry 1.0 to Industry 4.0.
Industry 1.0 is the first industrial revolution which began in England in the 18th century, covering more or less the period between 1770 to 1840, almost 300 years ago. By the end of the 18th century, this industrial revolution had already spread to the British colonies including America. The core of this first industrial revolution was the mechanization of production, the replacement of human or animal work with machines. It was also the beginning of the vast usage of steam power. The Industrial Revolution (IR) 1.0 marked the first major transition from a handicraft economy to one involving the use of machines in the manufacturing processes.
It is clear from the present situation of the Philippine economy that we have not completely transitioned to IR 1.0. In the agricultural sector, there is still a widespread use of human or animal effort in the various phases of farming and not to mention in the transport of goods. In the fabrication of goods, especially in clothing and household goods, the handicraft economy is still prevalent. We still have to depend on the handicraft sector for poverty eradication rather than for significantly increasing our per capita income. This is also true for the small farming sector. The government efforts to help them with infrastructure and other support services are predominantly oriented towards poverty reduction rather than an increase in agricultural productivity. Only large-scale production of goods in the manufacturing or agricultural sectors through increased mechanization will result in big increases in our GDP per capita.
The industries that were impacted by IR 1.0 included the glass, mining, agriculture, and textile sectors. For example, before the first industrial revolution, threads for textiles were manufactured at home using simple spinning wheels. The basic tools, materials and equipment used to make the textiles were usually provided by merchants. The need to use tools made it difficult to manage production and to produce large quantities of items with the desired quality. With the onset of IR 1.0, mechanization was introduced into the production process, leading to faster turnarounds and relatively large-scale production. In fact, the mechanized version of textile making led to a total production that was eight times more in volume than the former production process.
While steam power was already known, it had not yet begun to be utilized in manufacturing. When its usage was introduced in industry, it was considered the biggest breakthrough ever accomplished during this era. Not only did steam power lead to the production of larger volumes, it also led to a significant increase in the productivity of labor, making possible the granting of higher wages. For example, rather than employing people to power weaving looms, steam engines were used to provide adequate power for the machines. In sum, the landmark technologies that characterized IR 1.0 were the machines powered by water and steam, such as the mechanized weaving loom that was first developed in 1784. Other machines that were invented during this period included the water wheel, more complex spinning wheels, and the steam engine.
These newly invented machines allowed workers to produce goods in large quantities, enabling economies of scale that reduced the cost per unit of the products. This allowed small businesses to grow and to develop larger organizations that served larger markets. The two sectors that benefited most were the textile and transport industries. These benefits were enhanced further when coal began to be used as an additional source of fuel for different manufacturing processes.
The dark side of IR 1.0, exposed in the famous novels of Charles Dickens, was the greater demand for the production machines than could be produced. After all, these machines had just been invented and it took some time before they could be mass produced. The consequence was that there were relatively fewer machines and technologies to meet the swelling demands of a rapidly growing population. Ironically, this situation led to greater pressure on workers who were forced to work for longer hours to make fuller use of the scarce machines and often under unhealthy working conditions. Even more tragic was the use of child labor and even pregnant mothers to supplement the working hours of the employed labor force.
Such abuses precipitated the revolt of the masses and the ascendance of the anti-capitalist doctrine of Karl Marx who predicted the demise of capitalism. These abuses also led to the articulation of the social doctrine of the Catholic Church by Pope Leo XIII who wrote the first social encyclical entitled Rerum Novarum which defined the human rights of workers to just wages and humane working conditions. On the part of civil authority, in 1833, the Factory Act was put in place in the United Kingdom to ensure that high standards were followed in all workplaces, guaranteeing the safety, health, and protection of all employees and prohibiting, among other malpractices, child labor.
The second industrial revolution (IR 2.0) began in the 19th century, around the 1870s. The main engine of this industrial revolution was the development of machines running on electric energy, especially in Britain, America, and Germany. Electric energy was already being used as a primary source of power. Electric machines were more efficient to operate and maintain, both in terms of cost and effort, compared to water and steam. Those using water and steam were comparatively inefficient and resource hungry. The first assembly line was also built during this era, further streamlining the process of mass production which became a standard practice.
Another notable feature of IR 2.0 was the improvement in the industry culture. Even today when factories are moved to the countryside in the Philippines, managers face the hard challenge of changing century-old habits nurtured in a rural setting such as lack of punctuality, the so-called mañana habit of postponing things for tomorrow, the lack of attention to exactness in the smallest details of work (medyo tama, medyo mali, puede na — a little right, a little wrong, that will do) and too much socializing in the work place.
During IR 1.0, management programs were introduced through the Factory Act of 1833 in England. These programs not only ensured that manufacturing facilities were highly efficient but also ensured that employees worked for reasonable hours and were protected from abuse.
The Philippines experienced IR 1.0 and IR 2.0 without having completed the necessary stage of the agricultural or green revolution that England and other large nations went through. This happened at the beginning of our industrialization efforts in the 1950s and 1960s during which time manufacturing grew at an average of 12% annually, stimulated by import restrictions. The problem was that we lingered too long at the import-substitution and protectionist stage of industrialization. Our East Asian neighbors also had their stage of import-substitution industrialization. But in less than a decade, they knew how to transition to the more profitable export-oriented industries that were encouraged by their respective governments through the appropriate market-oriented policies. As we shall see in the subsequent articles, our inability to take advantage of our demographic dividend by transitioning to an export-oriented industrialization strategy led to a significant slowdown in Philippine manufacturing from which we are still trying to recover.
When and how can Philippine manufacturing recover its former growth?
(To be continued.)
Bernardo M. Villegas has a Ph.D. in Economics from Harvard, is professor emeritus at the University of Asia and the Pacific, and a visiting professor at the IESE Business School in Barcelona, Spain. He was a member of the 1986 Constitutional Commission.